A new development has rarely been as successful as the HERBOLD SB series granulator with force feeding device. With this granulator design the infeed material is fed by force into the grinding chamber with the help of horizontal feeding screws.
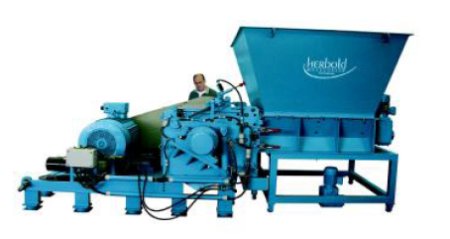
Photo 1: SML SB 60/145
The great demand for this new design is really not surprising: this new grinding principle saves energy up to 50 %, the throughput is twice or three-times as high compared to standard gravity-fed granulators.
Worn-out knives are the reason when the material “dances” on traditional machines: the rotor is then no longer capable of seizing the grinding material neatly.
This is excluded with this new design: due to the force feeding device, there is always exactly the very quantity of material between rotor and stator knives that corresponds to an optimal loading of the granulator. This is achieved by an intelligent link of the granulator’s energy uptake and the number of revolutions of the screw.
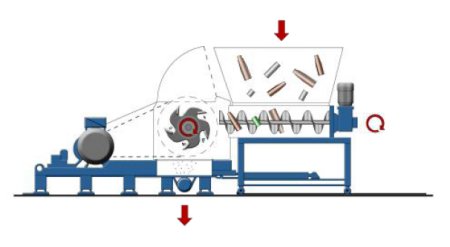
And there are other advantages:
- An intermediate buffer is installed above the screws and thus contributes to an increased optimal loading of the granulator, especially, if a shredder with an oscillating pressure ram is placed in front of the granulator: a more even flow into the granulator is guaranteed due to this buffer what again results in a higher throughput.
- A smaller-sized granulator is possible: this means that less space is needed; the wear parts are cheaper and can be exchanged much faster.
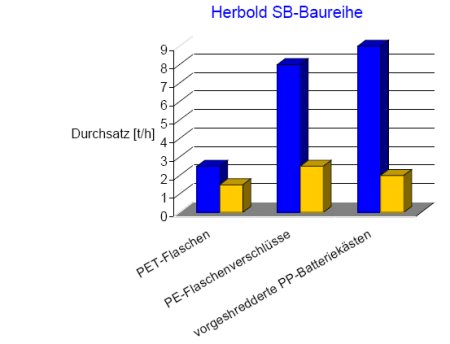
Photo 3: Performance of our Herbold SB Series Granulator (blue bars) with a rotor diameter of 600 mm and a rotor width of 1000 mm in comparison to a traditional granulator.
- Grinding causes less dust since the material is not unnecessarily whirled around in the grinding chamber. Especially for the grinding of bottles but also with pre-shredded waste, this granulator means real progress. Above all, the enormous energy savings in connection with other savings make the use of this machine economical in a few months only.