Washing and Separation Plant
A Newly Developed Washing and Separation Plant for Treating Polypropylene Resulting from Lead Reclaim from Car Batteries.
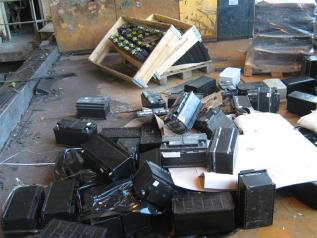
Fig. 1: casing parts
A polypropylene fraction remains once the old car accumulators have been size-reduced and the acid as well as the accumulator grids treated. The fact that the material is contaminated with residues from earlier processing steps makes its recycling more difficult. The material is acid-contaminated, mingled with rests from wooden pallets and mixed with mineral foreign bodies. Some of these contamination types are water-soluble, others are not, partly specifically heavier than PP, partly also lighter.
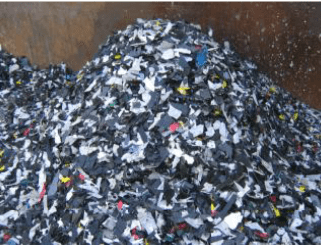
Fig. 2: size reduced casing parts
The procedure for this recycling problem developed by Herbold’s design engineers comprises three steps:
Wet size-reduction
A granulator with a screen insert, working with a great amount of water, size-reduces the casing parts that have already coarsely been shredded in upstream production steps. The intensive mechanic strain during the grinding step cleans the material and makes sure no dirt particles adhere to it. A downstream dewatering screw separates the ground material from the dirty water and rinses the end product with fresh water.
Wet separation
During this step, the specifically heavier PP fraction is separated from the lighter PP fraction. Remaining metals, mineral foreign bodies, hard rubber remnants from battery casings not belonging to the same type are separated with the help of this wet separation step.
Dry separation
Once the material has been dried, the specifically lighter foreign bodies are separated from the ground material: among these are wooden parts, fibres, films and the PP fraction. This is achieved with a multi-step system consisting of an air separator, a screening machine and a vibration separator. Its advantage: It also makes the separation of plasticized PVC foam seals (with y < 1) possible – a material fraction where wet separation will not work. Conventional accumulator scrap recycling systems have so far had difficulty in coping with this kind of scrap.
The plant has been designed for a throughput of 1,200 kilogram per hour. The total connected load is 145 kW (thermal drying included). The homogeneous PP fraction accordingly produced is free from dirt and foreign bodies. Therefore, the material is appropriate for the production of high-quality injection moulding parts such as covers for battery casings.
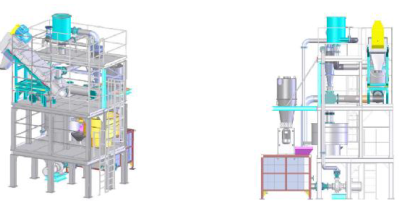
Fig.3 – 4:
A complete line was delivered to a German company and another one was recently commissioned in Ukraine.