For shredding of large-diameter, reject pipes: a completely new solution! The HERBOLD circular shredder of the ZSR serie Thick-walled PE pipes are continually growing in size: while 1600 mm used to be the common standard, dimensions of over 2000 mm are no longer any exception.
The production of such pipes with wall thicknesses sometimes over 100 mm and purgings weighing several 100 kg naturally results in rejects, which must be economically recycled. HERBOLD has taken a completely new approach to this problem: the circular shredder of the ZSR series.
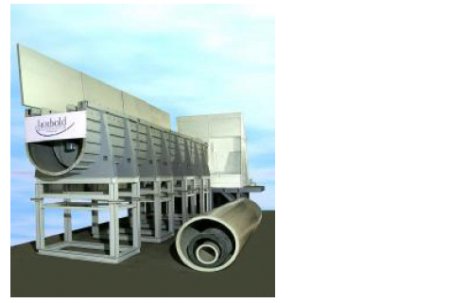
The material is deposited in a horizontal charging trough, which is equipped with a feed device on the front side. This feed device pushes the material deposited in the trough against an inclined disk rotor, which is equipped with special cutting tools. This rotor cuts the material into thick-walled chips, which are then crushed further in the following mill.
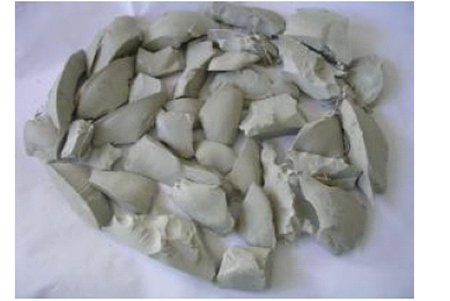
Photo 2: Optimum quality of the preliminary shredding
Only with such thick-walled chips can easily-flowing material with a high bulk density be achieved in the following cutting mill. The previous solutions on the market using single- or multiple-shaft shredders have significant disadvantages:
- The milling quality is inadequate because of the thin chips produced by the shredder: the material has poor flow properties, and often has to undergo a second granulation process in order to be fed in again.
- The pipes must either be placed vertically into the shredder shaft, several shredder shafts have to be engaged or there are other restrictions, e.g. in the pipe length, if these have to be fed in parallel Due to the working method of these systems, the performance is low, and the efficiency questionable.
With the HERBOLD circular shredder, these problems no longer exist:
- The achievable end-product consists of a material with excellent flow properties with high bulk density, and a low proportion of fines, which can easily be transported and used in conventional systems.
- Pipes of 6 m, 12 m or even longer can be fed in horizontally and processed without preliminary cutting. The feed trough is closed and locked by means of a cover before the shredding process starts: this procedure prevents the danger of accidents and foreign bodies accidentally falling into the trough.
- The throughput performance is very high, with even the smallest machines achieving a performance of 1.5 to 2,5
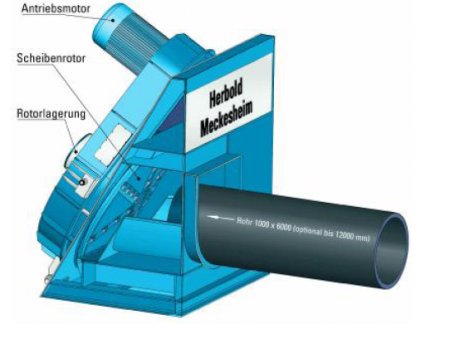