Recycling of composite materials
Composite materials such as metal and plastics or plastics and glass fibre composite materials are very popular: It is easy to produce lighter material-saving parts with these compound materials. The recycling of the emerging production waste has also to be taken into consideration – as well as the recycling of post-consumer parts. With the latest state-ofthe- art technology from HERBOLD Meckesheim GmbH these materials can be sorted in a cost-effective way and recycled for reuse into homogeneous material categories with a high degree of purity.
The main focus is on the purity of all resulting fractions. Not only the more valuable part of the composite material is in the centre of interest, but the aim is an almost complete recycling of all components. Even the low-grade fractions, commonly buried in costly landfills, contain a value-creation potential.
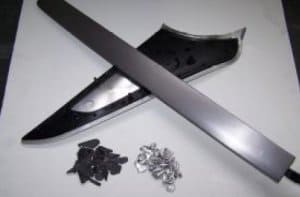
Fig. 1: example of recycling of composite materials
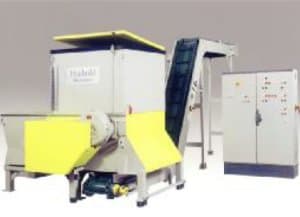
Fig. 2: Herbold Single-shaft and Two-shaft Shredder
This aim can be achieved with modern technology consisting of three steps:
- Pre-size-reduction if required by the dimensions of the parts. For this purpose, singleshaft and two-shaft shredders are available, able to cope with large amounts of material, making it thus possible to empty whole lattice box and container loads without the assistance of operators: the dosage is done by the shredder itself.
- The efficient impact crushing for separating the composite materials from each other by the effect of the impact. For this purpose, machines with a capacity between 22 and 250 kW are available.
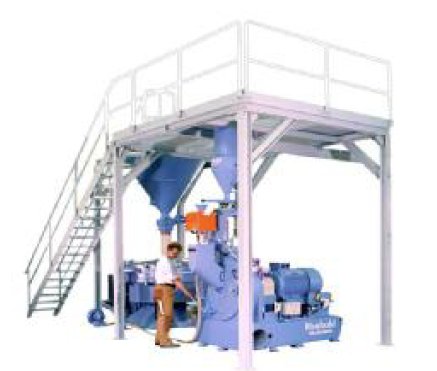
Fig.3: Herbold Pulverizer type PU500 with screening machine
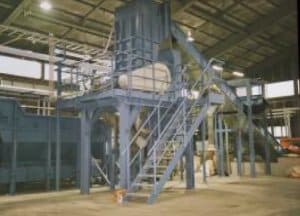
Fig.4: Washing line from Herbold Meckesheim
- A separation adapted to the material properties and requirements.
HERBOLD Meckesheim (www.herbold.com) has a decade-long experience in the construction of recycling lines for plastics. Besides the equipment for dry recycling, Herbold Meckesheim also manufactures systems for wet separation steps that are best appropriate for several separation processes in the field of composite materials. These may be small compact solutions for a few hundred kg/h but also systems for high throughputs with several tonnes per hour.
A technical laboratory divided into a wet processing department and a dry processing department is available in Meckesheim in order to carry out tests on full-scale demonstration machines and to find the specific solution best solving the customer’s recycling problem.
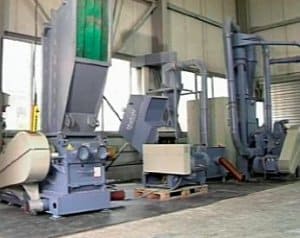
Fig. 5: Technical lab of Herbold Meckesheim GmbH