BOPET and BOPP films with heavily printed surface or metallized cannot be treated with traditional recycling processes, or at least only with great difficulty due to the high standards required for the degasification of extruders.
Herbold succeeded in finding a reliable solution: the HERBOLD plastcompactor. Thanks to its design as an “open” system, it can successfully cope with entirely printed or metallized films.
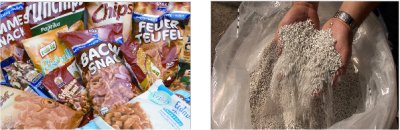
Fig. 1: Recycling of difficult material: Thin films with printed or metallized surface
Fig. 2: The end product: agglomerate with high bulk density and excellent flow properties
The HERBOLD plastcompactor transforms film waste in agglomerate with excellent flow properties and a very high bulk density that can then be further processed on injection moulding machines or extrusion plants similar to new material.
How does a HERBOLD plastcompactor work?
The material is continuously processed between a rotating and a stationary compactor disc, equipped with screwed-on exchangeable kneading bars. The pre-size-reduced material is continuously conveyed to the working zone through the centre of the stationary disc. The friction arising at and between the compactor discs very quickly heats the material, rendering it slightly sintered.
Afterwards, the heated material is fed to a hot melt granulator, turning it into agglomerate with good flow properties and a high bulk density.
The procedure is a particularly economic one and due to the automatic operation of the HERBOLD plastcompactor, www.herbold.com, no operators are needed. The densifier for plastics available in several sizes achieves a throughput performance between 100 and 1.400 kg/h.
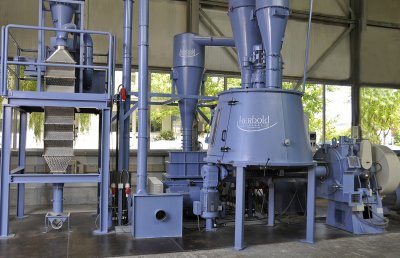
Fig.3: Herbold plastcompactor type HV 50
A typical representative of this size is the compactor HV 50 with a 110 kW drive and a throughput performance of approximately 800 kg/h with A-PET or PET-G. There is a positive side effect when processing PET film: the material is crystallized at the same time.
Besides the treatment of uncontaminated waste, the HERBOLD plastcompactor can also be used downstream of a washing line for contaminated waste: here the material is dried at the same time, a process that can very easily and effectively be achieved with very thin LLDPE films or with LLDPE stretch films.