HERBOLD MECKESHEIM GmbH in hall 15 booth D 31
HERBOLD MECKESHEIM: Post consumer recycling –more efficient and economic recycling
In Milan, the manufacturer of machines and plants from Meckesheim/Germany will present new solutions for washing, separating and drying of plastic waste featuring low operating costs and higher efficiency.
In the front of the line is the HERBOLD wet shredder HGM: beginning at the pre-size reduction step water is added, which is new. Until recently, water was only used in the granulation process where further size reduction occurred. Approximately 25 years ago, Herbold made the wet granulation technique marketable and with it set standards in the industry. The advantages of wet granulation are obvious; less wear and tear, no plastification due to the optimum cooling during the size reduction process, and a very effective separation from the first processing step.
Above all, this technique is well suited for highly contaminated material such as agricultural film (fig. 1). It is also suitable for post-consumer film from households and wet granulation has significantly increased the life between knife changes enabling a more economic operation. Even problematic material such as wood and paper fractions inside the input material can be handled better through the wet shredding as water allows for liberation from the material early on in the process (fig. 2).
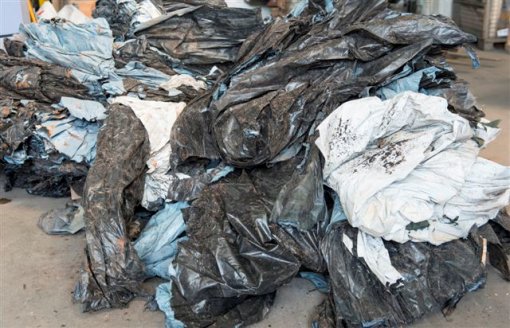
Fig. 1: Contaminated agricultural film
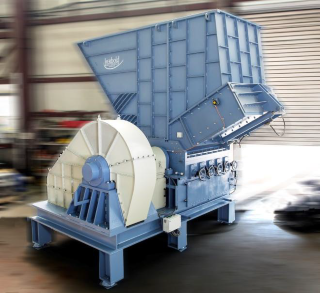
Fig. 2: Herbold Granulator HGM
Lowering the operating costs is another main focus and wear protection assists in it. No longer is there time-consuming armoring of the machines with long downtimes as Herbold’s product range included granulator housings equipped with exchangeable wear plates.
This shortens the downtown and increases the life of the granulator as the wear plates can be replaced quite easily in comparison to rebuilding the housing. Now there is also the possibility to exchange the wear plates for rotors; the blade carriers can be unscrewed if required (fig. 3). In cases of wear this will eliminate the need to disassemble, rebuild, and balance the rotor.
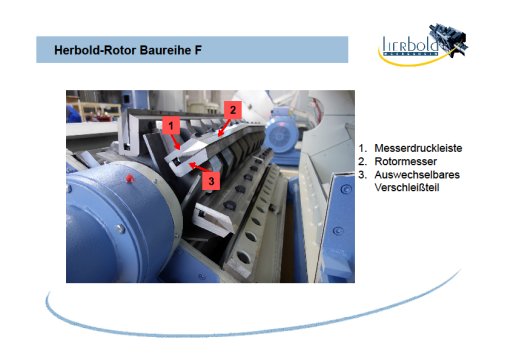
Fig.3: Herbold rotor
The HERBOLD plastcompactor is a solution for turning film, fibers, and foams with low bulk densities into an agglomerate with high bulk density and excellent flow properties (fig. 4). The plastcompactor at the end of the wash line offers two benefits: the higher bulk density and free-flowing properties and acts as a very efficient drying step. With this material it is possible to homogenize large loads of 20 tons in order to produce the required product properties. The HERBOLD plastcompactor has advanced and can handle capacities up to 1,500 kg/hr.
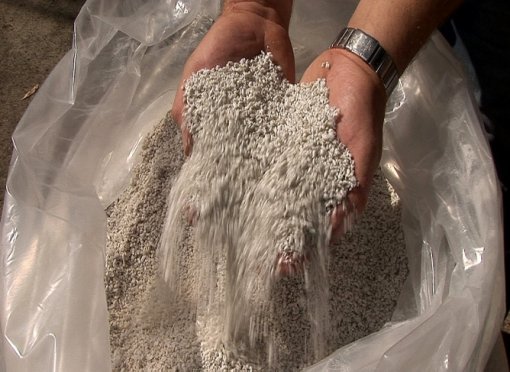
Fig. 4: Agglomerate with high bulk density
In the new technical center in Meckesheim near Heidelberg, extensive enhancements were carried out to be able to run tests with customer’s original material in industrial scales. There HERBOLD offers the possibility to demonstrate all process steps belonging to a washing and agglomeration plant. This enables already in the project stage a provision of samples even in larger amounts considerably facilitating investment decisions.